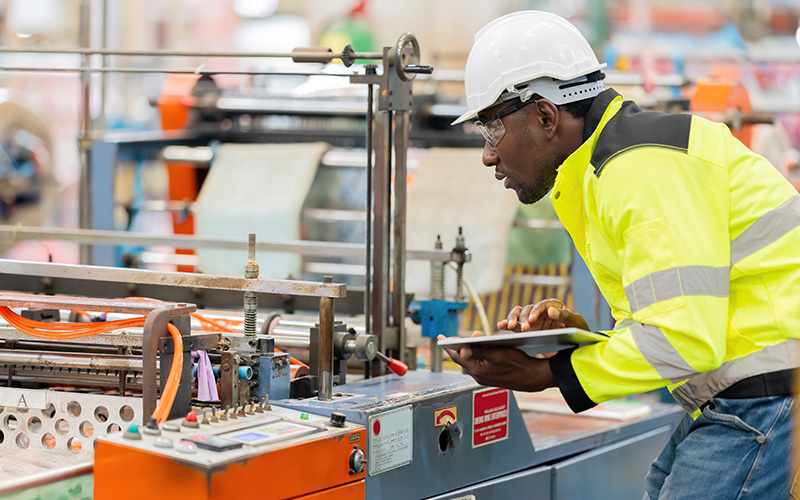
In today’s competitive manufacturing environment, Maintenance, Repair, and Operations (MRO) have become pivotal in determining a company’s productivity and overall performance.
well-structured approach to maintenance can significantly improve Overall Equipment Effectiveness (OEE) and drive profitability. Your maintenance department can become crucial to your success with the right tools and strategies.
Through our Digital Production System (DPS), we help manufacturers optimize maintenance strategies by providing real-time insights, predictive analytics, and AI-driven decision-making tools. This guide will walk you through the top five strategies for transforming your maintenance department with DPS to improve uptime, throughput, capacity utilization, and profitability.
But before we discuss actionable steps, assessing your current maintenance approach is essential. Are you constantly reacting to breakdowns or have a strategic, data-driven system? No matter where you are, DPS offers solutions that will enhance your maintenance processes starting today.
Maintenance Approaches Compared
Before building an improvement plan, it’s crucial to understand where you currently stand. Maintenance approaches can vary widely depending on your organization’s structure and goals. Let’s explore the most common methods:
1Reactive Maintenance: Fix It When It Breaks
Reactive maintenance, or the “run-to-failure” method, is simple—repairs are made after a breakdown occurs. While this approach requires less upfront planning, it can lead to unpredictable downtime and higher costs, making it unsuitable for critical equipment. With DPS’s real-time monitoring, manufacturers can transition from reactive to proactive maintenance, reducing the likelihood of sudden breakdowns.
2Preventive Maintenance: Scheduled Upkeep
Preventive maintenance involves scheduling repairs or part replacements before failures occur. This method can improve reliability but may lead to unnecessary replacements. DPS helps optimize this process by tracking equipment usage and performance data, ensuring that preventive actions are taken only when truly needed, saving time and resources.
3Usage-Based Maintenance: Tailored to Machine Activity
In usage-based maintenance, parts are replaced based on how much the machine has been used. While more specific than preventive maintenance, it requires precise tracking of machine hours. DPS simplifies this by automating usage tracking ensuring accurate replacement schedules.
4Condition-Based Maintenance: Monitoring Wear and Tear
Condition-based maintenance focuses on replacing parts based on wear rather than time or usage. With DPS’s IoT sensor integration, real-time data on equipment conditions can trigger maintenance when needed, minimizing downtime and maximizing asset life.
5Predictive Maintenance: Anticipating Failures
Predictive maintenance uses AI and historical data to forecast when parts will fail, reducing downtime and repair costs. DPS’s AI-powered predictive tools analyze equipment performance and provide accurate failure predictions, allowing your team to act before problems escalate.
6Prescriptive Maintenance: Choosing the Best Action
Prescriptive maintenance goes beyond forecasting failures—it analyzes potential actions and provides the best course based on factors like safety, quality, and timing. DPS uses advanced analytics to recommend optimal maintenance strategies, ensuring your team always makes the best decision for long-term operational success.
Five Key Steps to Improving Maintenance with DPS
Now that we’ve reviewed common maintenance strategies let’s explore five actionable steps you can take today to transform your maintenance department using DPS.
1Implement Total Productive Maintenance (TPM)
Total Productive Maintenance (TPM) integrates maintenance with daily operations, encouraging employees to take ownership of equipment care. With DPS, TPM becomes even more effective by providing real-time insights into machine performance and encouraging proactive involvement from your workforce.
- Employee Training: Use DPS’s training modules to ensure employees understand the equipment and can identify potential issues early.
- Create Cross-Functional Teams: Establish teams that include maintenance specialists and production operators, ensuring that maintenance becomes an integrated part of daily operations.
- Continuous Improvement: DPS’s built-in feedback tools allow teams to track and measure the effectiveness of maintenance initiatives, making continuous improvement a reality.
Key Benefits of TPM with DPS:
- Increased employee engagement in maintenance
- Proactive issue identification through real-time data
- Continuous improvement of maintenance practices
2Enhance Scheduling and Coordination
Proper scheduling and coordination are critical to reducing downtime and improving maintenance efficiency. DPS’s scheduling features allow maintenance tasks to be planned in sync with production schedules, avoiding conflicts and minimizing downtime.
- Utilize Real-Time Scheduling: DPS enables you to create dynamic schedules that adapt in real-time, ensuring maintenance tasks don’t interfere with production.
- Foster Communication: DPS facilitates direct communication between production and maintenance teams, keeping everyone aligned on schedules and priorities.
Key Benefits of Scheduling with DPS:
- Minimizes scheduling conflicts with production
- Ensures real-time updates for better coordination
- Increases overall efficiency by aligning maintenance and production needs
3Optimize Labor and Overtime Management
Managing labor and overtime is essential to maintaining a productive workforce. DPS provides detailed insights into staffing needs, allowing you to make informed decisions about shifts, overtime, and labor allocation.
- Track Labor Utilization: DPS tracks real-time labor usage, identifying areas where staffing levels need adjustment to avoid excessive overtime.
- Develop Efficient Shifts: Use DPS’s data to create shift strategies that balance workload and ensure optimal coverage.
Key Benefits of Labor Management with DPS:
- Reduces unnecessary overtime by optimizing shift schedules
- Improves workforce productivity through better labor allocation
- Enhances decision-making with real-time labor tracking
4Drive Efficiency and Cost Reduction
Efficiency and cost reduction are at the heart of any successful maintenance strategy. DPS helps identify inefficiencies in your maintenance processes, enabling you to make data-driven decisions that reduce costs and improve performance.
- Conduct Regular Audits: Use DPS’s reporting tools to audit maintenance activities regularly, identifying inefficiencies and areas for improvement.
- Implement Lean Principles: DPS’s data analysis tools allow you to apply lean manufacturing principles, streamline processes, and reduce waste.
Key Benefits of Cost Reduction with DPS:
- Identifies waste and inefficiencies through detailed audits
- Applies lean principles to enhance operational efficiency
- Provides real-time data to make informed cost-saving decisions
5Leverage Advanced Technology
Integrating modern technology into your maintenance department is essential for staying competitive. DPS’s IoT sensors, AI, and predictive maintenance tools provide real-time data and actionable insights, allowing you to transition from reactive to predictive maintenance strategies.
- Use IoT Sensors: DPS integrates IoT sensors to continuously monitor equipment health, providing real-time data for condition-based and predictive maintenance.
- AI and Machine Learning: Leverage DPS’s AI capabilities to predict equipment failures and prescribe the best action, reducing unplanned downtime.
Key Benefits of Technology Integration with DPS:
- Real-time monitoring of equipment through IoT sensors
- AI-driven predictions to anticipate failures and suggest actions
- Enhanced maintenance efficiency and reduced downtime
Unlock the Full Potential of Your Maintenance Department with DPS
Maintenance in manufacturing is no longer just about fixing equipment when it breaks—it’s a strategic function that directly impacts productivity, profitability, and operational efficiency. With DPS from POWERS, manufacturers can transform their maintenance departments into high-performing, efficiency-driven teams contributing to the bottom line.
By integrating real-time data, AI-powered predictive maintenance, and seamless collaboration tools, DPS ensures that your maintenance operations are proactive, efficient, and aligned with your overall business goals.