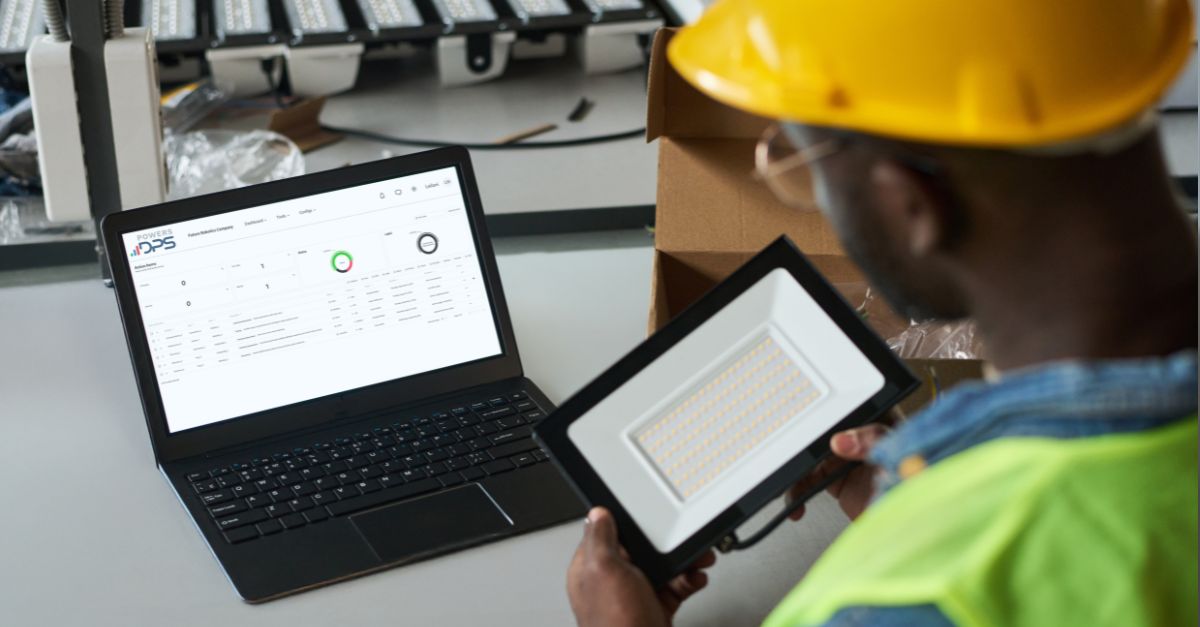
Continuous improvement in manufacturing isn’t just about identifying gaps—it’s about taking action and following through. Without a structured system to track corrective actions, issues get lost in the shuffle, accountability weakens, and progress stalls.
That’s where Action Item Logs come in. These structured task trackers help teams prioritize, assign, and complete actions that address performance gaps, maintain operational discipline, and drive continuous improvement.
What is an Action Item Log?
An Action Item Log is essentially a task tracker built for structured problem-solving. While “tasks” can be broad, Action Items are specific, scoped to a goal or project, and always have:
- A clearly defined owner – Someone accountable for completing the action.
- A due date – Ensuring timely follow-up and execution.
- A clear objective – A defined corrective action or improvement step.
In manufacturing, Action Item Logs are critical to closing process gaps and maintaining a continuous improvement workplace culture. They allow teams to identify, track, and resolve issues that impact production, safety, quality, and efficiency.
How Action Item Logs Drive Continuous Improvement
1Enhancing Accountability
Without structured follow-up, improvement efforts fall apart. Action Item Logs assign clear ownership so every corrective action has an accountable leader and a deadline for completion. This keeps front-line leadership engaged and ensures that no task slips through the cracks.
2Prioritizing & Addressing Process Gaps
In fast-paced manufacturing environments, gaps in production systems can go unnoticed or unaddressed due to a lack of tracking. A well-maintained Action Item Log ensures that:
- Issues are documented and prioritized for resolution.
- Process improvements are clearly outlined and assigned to the right team members.
- Teams can focus on high-impact corrective actions rather than firefighting daily issues.
3Streamlining Problem-Solving & Root Cause Analysis
Sustainable improvements come from solving root causes, not symptoms. Action Item Logs help teams:
- Identify and track corrective actions for recurring problems.
- Follow up on solutions to measure their effectiveness.
- Avoid repetitive issues by documenting successful resolutions.
4Improving Cross-Team Collaboration
Many manufacturing challenges span multiple departments—maintenance, production, quality, and supply chain. A structured log keeps everyone informed about open actions, preventing misalignment and ensuring faster resolution.
5Reinforcing a Workplace Culture of Continuous Improvement
A robust Action Item process doesn’t just fix problems—it creates a mindset of accountability and execution. When employees see their improvement ideas captured, assigned, and completed, it encourages engagement, proactive problem-solving, and long-term operational excellence.
Best Practices for an Effective Action Item Log
To make Action Item Logs a valuable tool rather than just another spreadsheet that gets ignored, follow these best practices:
1Set Realistic Deadlines
- Action Items should have clear due dates that are both achievable and meaningful.
- Deadlines that are too short can lead to rushed, poorly implemented fixes, while deadlines that are too far out can result in low urgency and inaction.
- Consider the complexity of the task—some actions may require immediate resolution (e.g., safety hazards), while others involve longer-term process improvements.
2Define Ownership Clearly
- Every action item should have a specific, named individual responsible—not just a department or team.
- Ownership creates clear accountability—if multiple people are assigned, it’s easy for tasks to be ignored.
- In manufacturing, the best practice is to assign action items to a leader who has the authority to implement the change, rather than a frontline operator who may not have decision-making power.
3Regularly Review Progress
- The best Action Item Logs are not static—they should be a core part of daily or weekly team meetings.
- Regular check-ins ensure actions don’t get lost in the shuffle and allow teams to remove blockers before they delay progress.
- Leadership should track completion rates, overdue items, and recurring issues to refine processes over time.
4Document Results & Lessons Learned
- A completed Action Item doesn’t mean the process ends—documenting results and lessons learned ensures continuous improvement.
- Capture:
- What was fixed? (Problem and solution summary)
- Did the action work? (Was the issue permanently resolved?)
- What could be improved? (Adjustments for future situations)
- This historical record helps teams avoid repeating mistakes and builds a knowledge base for future problem-solving.
By following these best practices, Action Item Logs become a powerful tool for execution, visibility, and continuous improvement—not just another list of tasks that go unnoticed.
Why DPS’ Action Item Log is a Game-Changer
While many manufacturers rely on Excel spreadsheets to track Action Items, these fragmented systems lead to version control issues, siloed data, and lack of visibility.
DPS takes Action Item Management to the next level by:
- Automating Action Item Tracking – No more scattered spreadsheets; manage all corrective actions in one centralized system.
- Enabling Real-Time Collaboration – A conversation-style commenting system lets teams discuss and track progress directly within the platform.
- Supporting File & Media Attachments – Add supporting documents, photos, or deliverables to Action Items for better record-keeping and follow-through.
- Providing Full Visibility Across the Organization – Instead of isolated lists in different departments, DPS creates a single source of truth for all action items across the company.
By eliminating manual tracking inefficiencies and empowering teams with automation, DPS’ Action Item Log ensures that corrective actions are completed on time and drive real improvements.
Conclusion
A well-maintained Action Item Log isn’t just a checklist—it’s a tool for real change. By assigning ownership, tracking progress, and ensuring follow-through, manufacturers can turn corrective actions into lasting operational improvements.
If your organization is still managing Action Items through disconnected spreadsheets, it’s time for an upgrade. DPS’ centralized Action Item Log simplifies execution, increases visibility, and makes continuous improvement a daily reality.