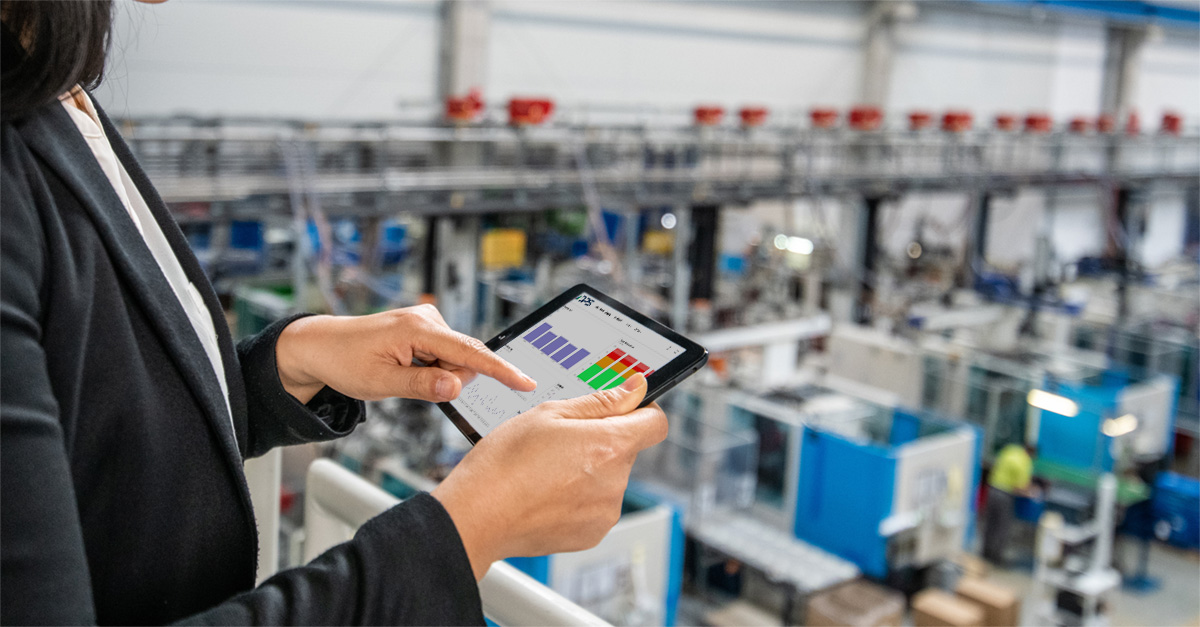
Every plant deals with downtime. Some of it’s expected. Most of it isn’t.
But what many leaders don’t realize is this: downtime, especially when it starts showing up as a pattern, is trying to tell you something.
If your team is only reacting to each event as it happens, you’re stuck in firefighting mode. That might solve today’s issue, but it won’t prevent tomorrow’s.
And when you use DPS, those trends are no longer buried in spreadsheets or siloed between departments. They’re visible in real-time, and they help your teams take action faster and smarter.
Not All Downtime Is Created Equal
Most operations are already tracking downtime in some form, usually focused on the big mechanical failures that stop production. But there’s a lot more to the story. What often gets missed is hidden lost time, the performance that disappears even when there’s no obvious breakdown.
That’s where most plants fall short. They aren’t measuring actual performance against capacity, so they don’t see the small stops, slow cycles, or missed targets that add up to major losses over time.
The platform gives you visibility into both lost time events and capacity performance, side by side. That helps frontline teams stay focused on where the real leaks are happening, even when everything “looks fine” on paper. Once those gaps are found, they can be captured and tracked as downtime events, helping build a clear case for action.
And DPS doesn’t leave you digging through raw data. As soon as events are logged, they’re automatically organized into Pareto charts, your top 10 issues by total time lost or by total number of occurrences. That way, you can spot:
- Major issues that demand urgent attention
- Frequent small events that quietly erode output
Instead of chasing noise, your team can stay locked in on the biggest opportunities for improvement, fast.
Patterns Point to Priorities
If you want to boost uptime, the answer usually isn’t “work harder.” It’s “work smarter with the facts in front of you.” And the smartest place to start is with the patterns you’re already experiencing, whether you see them or not.
DPS helps shine a light on patterns that might otherwise be dismissed as one-off problems:
- That same filler goes down every Wednesday night on second shift, why?
- One line loses 15 minutes every day to a manual process that no one questions anymore
- Maintenance logs show repeat failures, but no one's connected the dots on the root cause
These aren’t isolated incidents. They’re signs. When trend data makes them obvious, your team can move from reacting to actually preventing. That’s the turning point.
From Daily Trends to Long-Term Wins
The real value in tracking downtime trends isn’t just knowing what’s going wrong. It’s being able to do something about it, before it spirals.
Let’s say the data shows excessive delays during changeovers on Line 2. You now have hard evidence to:
- Launch a focused kaizen event on that line’s changeover process
- Update your work instructions or retrain teams on standard changeover procedures
- Work with maintenance to adjust preventive maintenance timing
- Rethink the schedule to better match high-skill operators with high-variance setups
This is where real continuous improvement begins. No guesswork. No hunches. Just data-backed decisions that actually move the needle.
And when that kind of discipline is repeated across lines and teams, it doesn’t just reduce downtime, it transforms performance.
Built for the Frontline, Not Just the Front Office
Frontline leaders use their recent performance trends to guide their huddle meetings and set the day up for success. They can spot what’s trending, flag issues early, and align the team around the top priorities, all before first break.
At the same time, plant leaders and CI teams use the same data to identify longer-term improvement opportunities, track progress, and hold the gains.
Whether you’re solving today’s problems on the floor or analyzing the last 30 days in a staff meeting, DPS makes sure everyone is working from the same source of truth.
Downtime Trends Are a Mirror Take a Look
You don’t need more data. You need clearer insights from the data you already have, and a system that puts it to work for you, not against you.
Downtime data is collected automatically, organized instantly, and available the moment an event occurs. That means your team can act on it while it still matters, not days or weeks later.
Downtime trend analysis through DPS gives you a real-time window into your operation’s weak spots, so you can spot performance gaps, prioritize improvements, and stay focused on what’s actually costing you time and output.
If you’re logging downtime but not using it to guide action, you’re not getting the full value from the effort. The opportunity is already there, you just need to make it visible.
Want to turn your downtime data into real results?
Our team helps frontline leaders and plant managers get more value from the DPS platform by focusing on what matters most. Let’s take a look at your trend data together and find the biggest opportunities for impact.
Ready to turn downtime data into real results?
Let’s talk about how DPS can help you spot the issues, prioritize action, and improve performance—starting today.