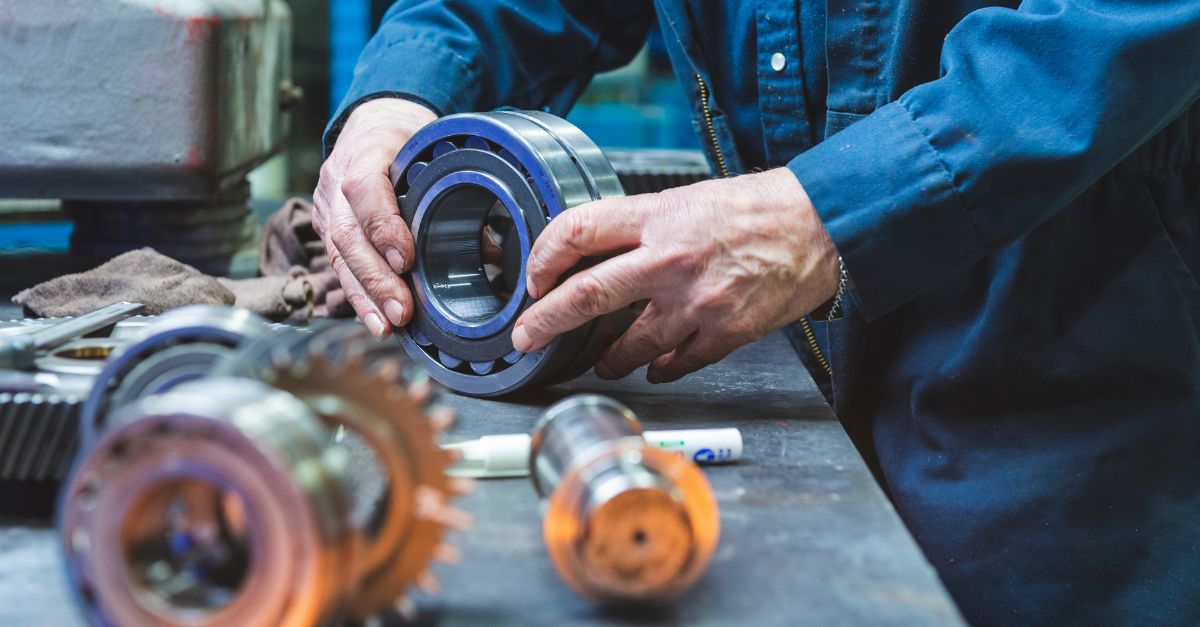
Not All Downtime Hits the Report
If you’re like most manufacturers, you’re tracking downtime through standard KPIs like OEE. And that’s a smart move, it gives you a high-level read on how equipment is performing across availability, performance, and quality.
But there’s a catch.
OEE is designed to show major disruptions. It picks up when a machine goes down or when output takes a measurable hit.
Things like short delays during changeovers, waiting on approvals, or searching for missing parts don’t always get logged. They’re not counted as downtime on paper, but they’re still downtime. And when these moments happen repeatedly throughout the day, across multiple shifts, across multiple lines, they add up fast.
If you’re only looking at OEE, you’re missing a huge part of the picture.
What OEE Misses
Traditional metrics give you a useful snapshot, but only a partial one. What’s missing is the context around what your team is actually dealing with on the floor.
OEE won’t tell you when:
- A supervisor spends 20 minutes chasing down a pallet tag or clarifying what’s supposed to run next.
- An operator is left waiting for someone to sign off on a quality check.
- A team gets stuck reworking a task because yesterday’s issue wasn’t communicated clearly.
- Maintenance is called, but no one knows who’s handling it, so the issue drags on.
None of these things show up in the system as formal downtime. And because they aren’t “big” enough to raise a flag, they often get brushed aside or forgotten entirely. But they’re exactly the types of issues that chip away at performance, drag out schedules, and lead to missed targets.
When these problems stay invisible, so do the opportunities to fix them.
This Is the Downtime That Slows You Down
This is the kind of downtime we see every day in facilities that are running full-speed, but still falling short.
The machines might be running. The people might be working. But there’s friction. And that friction comes from avoidable slowdowns:
- Delays in shift handoffs: When one crew doesn’t know where the last one left off, you lose time to confusion and double-checking.
- Task switching mid-run: When frontline leaders get pulled in different directions because of verbal instructions or unclear priorities, work gets interrupted.
- Extra steps and rework: When instructions aren’t standardized or communication breaks down, it causes redo work that could have been avoided.
- Waiting on decisions: When someone needs to make a call but the right person isn’t looped in, production pauses.
These issues don’t stop the line cold, but they do slow it down just enough to fall behind. And since no one is officially tracking it, it’s easy to assume people just need to “move faster” or “try harder.” But in reality, these are process problems, not people problems.
DPS Brings It to Light
This is where DPS makes the difference. It gives you visibility into the issues OEE can’t reach, without adding more reporting tasks to your team’s plate.
With DPS, your frontline leaders have a system that works in real time and connects directly to their daily responsibilities:
- Action Item Logs allow teams to quickly capture issues as they happen, whether it’s a delay, a miscommunication, or a resource gap. Nothing gets lost in the shuffle or forgotten after the shift.
- Escalation paths ensure that problems don’t stall out. The right people get notified, and the issue moves forward instead of sitting idle.
- Live updates across the platform keeps the entire team aligned, so decisions aren’t delayed and everyone’s working with the same information.
- Everything ties to the schedule, making it easy to see which issues impacted which jobs, areas, or metrics, and what needs to change moving forward.
With DPS, frontline leaders stop relying on memory or sticky notes. They gain a clear picture of what’s pulling time away from production, and they can use that insight to drive improvement.
Stop Letting Minutes Slip Away
The problem with hidden downtime is that it’s silent, but deadly to productivity. Teams don’t always realize how much time they’re losing to these “small” disruptions until they start tracking them. But once they do, the pattern becomes obvious.
That’s when things start to shift.
Instead of reacting to problems after they’ve done the damage, your team can get ahead of them. Instead of scrambling during peak hours, they’ve got clear routines, built-in accountability, and visibility into how the day is really going.
You’re lifting output, hitting goals more consistently, and creating time to improve processes instead of just managing problems.
Ready to See the Downtime That’s Been Hiding in Plain Sight?
If your team’s working hard but still missing the mark, the problem might not be effort, it might be visibility. DPS helps you uncover what your traditional metrics are missing and gives your team the tools to fix it at the source.