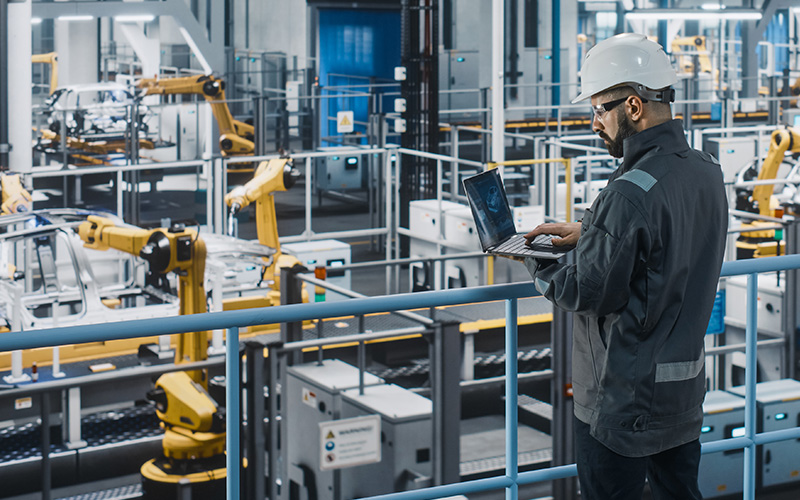
In the complex manufacturing world, every system and process is intricately linked, and the smallest failure in one area can ripple through the entire operation.
Nowhere is this more apparent than in Maintenance, Repair, and Operations (MRO). Proper maintenance is the cornerstone of operational efficiency, and yet, it is often an afterthought until something goes wrong.
These reactive strategies result in unplanned downtime, compromised production quality, and inflated operational costs, all eroding profitability. But with today’s rapid technological advancements, manufacturers are empowered to take a proactive stance.
Introducing DPS, the Digital Production System from POWERS—a next-generation manufacturing platform that delivers real-time, actionable insights to optimize maintenance processes, prevent costly failures, and significantly enhance productivity and profitability.
The Hidden Costs of Poor Maintenance
Poor maintenance practices can have far-reaching consequences, negatively affecting key metrics like Overall Equipment Effectiveness (OEE). OEE measures equipment efficiency by tracking availability, performance, and product quality—three areas directly influenced by how well equipment is maintained.
When maintenance is neglected, equipment downtime increases, performance lags, and product defects multiply. These issues hurt your bottom line, disrupt your production schedule, erode customer trust, and compromise safety. Here are some key ways poor maintenance impacts your operations:
- Downtime and Equipment Availability: Your machinery is offline every minute due to unplanned maintenance costs and valuable production time. Poor maintenance practices increase downtime and reduce equipment availability, which lowers your OEE score. This directly translates to lost productivity and delayed order fulfillment, harming your business reputation and customer relationships.
- Quality and Performance: Equipment that isn’t properly maintained often runs at suboptimal speeds and produces defective products. Over time, this leads to an increase in reworks, waste, and customer complaints. By failing to address these maintenance issues, manufacturers see a decline in product quality, ultimately impacting brand loyalty and profitability.
- Safety Risks: Faulty equipment is a major safety hazard. Poorly maintained machines are more prone to malfunctions, resulting in workplace injuries, safety violations, and regulatory fines. These incidents endanger employees and lead to costly downtime and increased insurance premiums.
The good news is that with the right tools and a proactive approach, you can turn maintenance into a powerful driver of productivity. DPS is designed to help manufacturers streamline maintenance processes, optimize asset performance, and drive sustainable growth across the entire production cycle.
How DPS Transforms Maintenance with Real-Time Data
Traditional maintenance approaches rely on reactive strategies—waiting for equipment to break down before addressing the issue. While this approach may work in the short term, it’s not sustainable. The longer manufacturers wait to fix equipment, the more likely problems will compound, leading to extended downtimes and higher costs.
DPS changes the game by providing real-time production insights and giving your team the information they need to make informed decisions. This AI-powered platform enables proactive maintenance, allowing teams to identify and address issues before they lead to costly failures. With its intuitive dashboard and advanced analytics, DPS delivers insights that help manufacturers:
- Optimize Overall Equipment Effectiveness (OEE): DPS tracks downtime, equipment performance, and product quality in real time, enabling teams to monitor the most critical aspects of OEE. By identifying patterns of underperformance or frequent failures, DPS allows maintenance teams to take corrective action before small issues escalate into significant problems.
- Reduce Unplanned Downtime: With DPS’s Downtime Tracker and real-time alerts, your team can quickly identify the root causes of equipment breakdowns and address them efficiently. This minimizes unplanned downtime and improves the predictability of your production schedule.
- Streamline Maintenance Tasks: The Action Item Log feature allows you to track and prioritize maintenance tasks, ensuring that nothing slips through the cracks. With DPS, your team can manage multiple maintenance workflows, track progress, and ensure timely resolutions to equipment issues.
By adopting DPS, manufacturers can transition from a reactive maintenance model to a proactive, data-driven strategy that boosts productivity, reduces costs, and enhances asset performance.
Leveraging AI for Smarter Maintenance Decisions
One of the standout features of DPS is its AI-powered analytics, which allows you to uncover hidden patterns in equipment performance and identify opportunities for improvement. The system continuously analyzes real-time data from your production floor, providing actionable recommendations for performance optimization.
For example, DPS can help you pinpoint when equipment is most likely to experience a failure, allowing you to schedule maintenance during planned downtimes. This predictive maintenance approach reduces the need for emergency repairs and extends your assets’ lifespan, improving your Return on Assets (ROA).
In addition, DPS helps your team prioritize maintenance tasks by analyzing which equipment failures significantly impact production. Focusing on high-priority issues allows you to allocate resources more efficiently and ensure that critical maintenance tasks are completed without delay.
Enhancing Safety and Compliance with DPS
Manufacturers must also prioritize safety and regulatory compliance, and DPS plays a critical role in ensuring both. The platform provides real-time visibility into equipment performance, allowing your team to monitor for potential safety hazards and take preventive action. Additionally, DPS offers built-in tools for documenting and tracking maintenance activities, ensuring that your operation complies with industry regulations.
Supporting Strategic Planning and Long-Term Growth
Beyond day-to-day maintenance management, DPS also offers powerful tools for long-term strategic planning. The system allows you to analyze historical data, compare performance trends, and make informed decisions about future equipment investments and upgrades.
With customizable scorecards, real-time communication tools, and AI-powered action planning, DPS supports continuous improvement initiatives and helps your team confidently plan for the future. Whether expanding production capacity or entering new markets, DPS provides the insights you need to scale efficiently and sustainably.
The Future of Maintenance is Here with DPS
In an industry where every second of downtime counts, having the right tools to manage maintenance is no longer a luxury—it’s a necessity. DPS empowers your team with the real-time data, advanced analytics, and actionable insights needed to take control of your maintenance processes and drive performance improvements across the board.
The Digital Production System from POWERS delivers more than just software; it offers a comprehensive solution built on decades of hands-on manufacturing expertise. With DPS, you’ll unlock the full potential of your equipment, streamline your operations, and set the foundation for long-term growth.